L’industria digitale resiste e rilancia: le tendenze del momento
Nel 2020 l’industria digitale italiana fattura 4,1 miliardi di euro e cresce dell’8%, nonostante lockdown, crisi economica e incertezze. Una prova del nove incoraggiante, per un mercato sempre meno potenziale e più reale. Questo, in estrema sintesi, il messaggio lanciato dalla ricerca 2020-2021 dell’Osservatorio Transizione Industria 4.0 della School of Management del Politecnico di Milano.
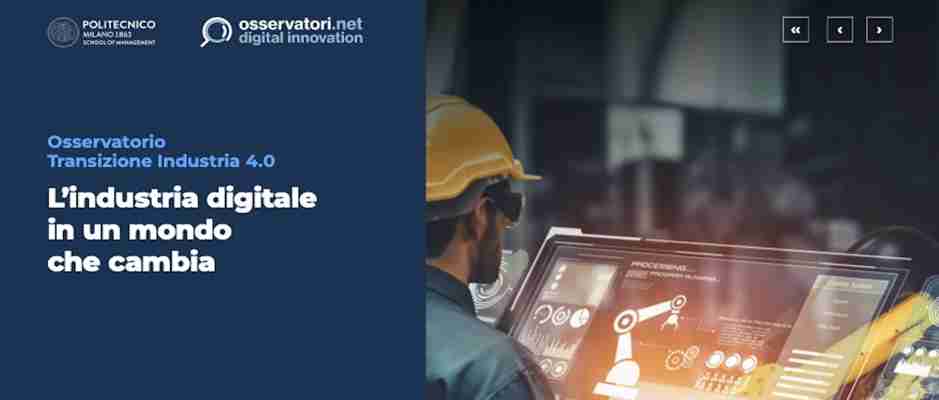
Una fotografia empirica di un mondo in costante movimento, di tecnologie smart che evolvono più velocemente rispetto alle persone e alle organizzazioni. Il covid-19 ha certamente accelerato la crescita digitale dei paradigmi aziendali, ma oggi è ancor più importante importante analizzarli per comprenderne esigenze e trend di sviluppo.
Industria digitale in un mondo che cambia
Al centro della trasformazione digitale del manifatturiero italiano ci sono il Piano Nazionale Transizione 4.0, le nuove consapevolezze generate dalla pandemia, l’Industrial Smart Working, il Green & Digital, la Servitization. Lo confermano i macro-temi sviscerati dall’Osservatorio Transizione Industria 4.0. “L’emergenza non ha arrestato la crescita dell’Industria 4.0 – spiega il responsabile scientifico Marco Taisch in apertura del convegno di presentazione della ricerca -. A conferma del fatto che non è stata una moda passeggera ma una progettualità che sta rinnovando il settore industriale italiano in modo. Le iniziative più semplici sono ormai conosciute e consolidate, con almeno un progetto attivato nel 75% delle imprese manifatturiere”.
Cosa manca per completare la convergenza digitale tra IT e operations? Per avviare progetti pervasivi, multi-tecnologici e basati sul cloud e reti innovative, è necessaria una visione di lungo termine. Ovvero sperimentare nuove applicazioni e investire nelle competenze 4.0 e nella formazione delle risorse aziendali.
Quanto vale Industria 4.0 in Italia
Come sta andando il mercato 4.0 e cosa ci riserva il futuro? Risponde Giovanni Miragliotta, direttore dell’Osservatorio Transizione Industria 4.0. “Il 2020 ha spinto le aziende a ripensare il modo in cui vengono gestite le operations. Remotizzazione, flessibilità e servizi diventano gli elementi chiave nella gestione dell’industria digitale. La resilienza della supply chain è ormai strategica per mantenere e aumentare la produttività delle aziende e per adattare la loro offerta alle sfide del mercato post-pandemia”.
Ecco la rappresentazione complessiva anno su anno delle cifre e delle applicazioni della fabbrica connessa.
Industrial IoT batte tutti
Come anticipato in apertura, il mercato italiano dell’Industria 4.0 nel 2020 ha toccato quota di 4,1 miliardi di euro. Un +8% trainato soprattutto dalle tecnologie IT, che coprono l’85% della spesa contro il 15% delle OT (Operational Technologies).
Gli investimenti delle imprese manifatturiere si concentrano prevalentemente in:
Industrial Internet of Things (connettività e acquisizione dati): 2,4 miliardi di euro, 60% della spesa totale;
Industrial Analytics: 685 milioni di euro, 17%;
Cloud Manufacturing: 390 milioni di euro, 8%;
servizi di consulenza e formazione: 275 milioni di euro, 7%;
Advanced Automation: 215 milioni di euro, 5%;
Additive Manufacturing: 92 milioni di euro, 2%;
Advanced Human Machine Interface: 57 milioni di euro, 1%.
Insomma, l’area più calda resta l’Industrial IoT, tecnologia abilitante importante anche grazie agli incentivi governativi. Bene, inoltre, il progressivo spostamento verso l’analisi e l’utilizzo dei dati (Industrial Analytics). In generale, permane un consistente gap tra grandi aziende e realtà imprenditoriali medio-piccole. Nelle pmi c’è ancora molto potenziale inespresso sul quale puntare nei mesi a venire.
Le applicazioni 4.0 più diffuse
Sul fronte delle applicazioni smart, in Italia nel 2020 si contano circa 1.400 sistemi di Industria 4.0 attivi nelle imprese manifatturiere, il 28% in più rispetto al 2019. Anche qui vincono le soluzioni di Industrial IoT – un quarto del totale (380, +31%) – spesso combinate con algoritmi di Analytics e Intelligenza Artificiale.
A seguire troviamo: le tecnologie Advanced HMI, come i wearable e le interfacce uomo-macchina per gestire i dati in formato visuale, vocale e tattile, con 286 applicazioni e un aumento del 15% e l’Advanced Automation (241, +5%), ovvero i sistemi di produzione automatizzati come i robot collaborativi. Particolarmente performante in termini di crescita sul 2019 il fronte Industrial Analytics, incentrato sulla previsione delle prestazioni di assetti industriali e processi produttivi, con 200 applicazioni e un +39%. Percentuali a doppia cifra anche per Cloud Manufacturing, monitoraggio e diagnostica degli impianti industriali da remoto (140, +33%) e Additive Manufacturing (125, +30%), diffuso principalmente nei settori automotive e aerospaziale.
Come andrà l’industria digitale nel 2021?
La crescita del mercato nel 2020 è stata inferiore alle stime presentate nel 2019 (+20%), ma ugualmente positiva visti i contorni socio-economici globali. Ecco perché gli analisti del Politecnico di Milano si sono “sbilanciati” con cauto ottimismo circa i numeri dell’anno in corso. Le previsioni per il 2021 indicano infatti un’ulteriore accelerazione della spesa, a un tasso compreso fra +12% e +15%, oltre i 4,5 miliardi di euro.
Tra i settori più performanti:
Cloud Manufacturing (+25-30%);
Advanced Automation (+15-20%);
Advanced HMI (+12-18%).
Meno sostenuta, invece, la crescita di Industrial IoT (+9-14%), Advanced Analytics (+12-16%) e Additive Manufacturing (+6-12%). Continua la diffusione dei servizi, per i quali si prevede un aumento del 10-15%.
Focus sul piano nazionale Transizione 4.0
Discorso a parte, meritato, per il piano nazionale Transizione 4.0, che si unisce al nuovo capitolo del PNRR dedicato alla digitalizzazione dell’industria italiana. Le opportunità di questo programma sono ben note alle aziende manifatturiere. L’83% delle 175 grandi imprese e pmi intervistate dall’Osservatorio conosce il credito d’imposta per gli investimenti in beni strumentali, il 55% quello per ricerca, sviluppo e innovazione e il 52% quello per la formazione.
Nei prossimi sei mesi, le esigenze più sentite sono:
sgravi fiscali sugli operatori per abbassare il costo del lavoro: 55%;
sugli operatori per abbassare il costo del lavoro: 55%; incentivi per l’assunzione di personale: 41%.
Nei prossimi due anni, invece, si auspica il rilancio di forme di iper e super ammortamento su beni strumentali (acquisto, revamping e accessori), indicato dal 48% del campione. Il 39% degli intervistati chiede poi incentivi diversi da quelli attualmente in vigore per gli investimenti in beni immateriali quali software e piattaforme per l’integrazione di sistemi. Certo, la differenza sarà fatta anche dal cambiamento di mindset e competenze: la formazione 4.0, secondo gli analisti dell’Osservatorio, è determinante a ogni livello e anche all’interno del board aziendale.
Sulle sfide del PNRR interviene infine Enrico Cereda, vice presidente di Assolombarda. “La carta vincente sarà il gioco di squadra – spiega il manager -. La realizzazione di un ecosistema pubblico e privato per fare leva sui 40 miliardi di euro a disposizione, sfruttando al massimo i piani nazionali di sviluppo della fabbrica connessa. Mi aspetto però procedure semplificate per gli imprenditori che credono in questo percorso e nell’ineluttabilità della trasformazione digitale delle imprese italiane”.
Post a Comment