Manifatturiero: cos'è, settori e futuro dell'industria manifatturiera
Cos’è l’attività manifatturiera
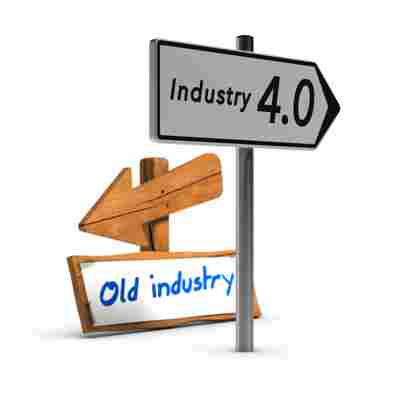
L’attività manifatturiera è un settore dell’industria che, sostanzialmente, trasforma le materie prime in prodotti finiti. In altri termini, l’attività manifatturiera (che si identifica con il settore manifatturiero) rappresenta l’attività umana mirata alla produzione di beni attraverso un meccanismo di trasformazione delle materie prime in oggetti destinati al consumo, ossia il prodotto finito o semilavorato, destinato a un’ulteriore attività manifatturiera. Ad esempio il prodotto della raffineria di allumina viene utilizzato per la produzione di alluminio di base; questo viene utilizzato negli impianti di trafilatura per fili di alluminio, utilizzati nelle unità manifatturiere che fabbricano prodotti fatti con fili di alluminio.
Il settore manifatturiero in Italia
Il Rapporto Competitività dell’Istat fornisce una fotografia dello stato del settore manifatturiero italiano. Secondo il rapporto, “sulla posizione competitiva del nostro Paese ha influito, nella prima parte del 2019, un andamento del costo del lavoro più vivace rispetto ai tre partner europei (in particolare per la componente degli oneri sociali). D’altro canto, la dinamica delle esportazioni in valore, seppure in forte rallentamento, è stata più brillante di quella di Germania e Spagna, e i beni italiani hanno aumentato le proprie quote di mercato in Francia, Belgio, Paesi Bassi, Svizzera e Stati Uniti mentre le hanno fortemente ridotte in Germania e in Spagna”.
Secondo l’Indicatore sintetico di competitività (ISCo), alimentari e bevande, abbigliamento, elettronica evidenziano un miglioramento competitivo rispetto alla media della manifattura sia nel 2018, sia nel 2019. All’opposto, tra i settori per i quali peggiora ulteriormente la condizione di relativa difficoltà competitiva si segnalano le attività del tessile, della gomma e del legno.
Nel corso del 2019 le imprese hanno fronteggiato una situazione di stagnazione della domanda. Tuttavia, nonostante il rallentamento dell’attività, le dotazioni di capitale e di lavoro hanno mantenuto una tendenza nel complesso favorevole, con una dinamica di poco inferiore a quella del 2018.
Nel rapporto si propone una “nuova tassonomia dei settori, le cui categorie individuano il tipo di trasmissione degli impulsi da e verso il resto del sistema economico”. Secondo questa classificazione, i comparti delle costruzioni e gli altri servizi di mercato risultano a trasmissione diffusa (propagazione estesa e veloce); nel sistema a trasmissione selettiva (trasmissione circoscritta ma veloce) rientrano gli alimentari e bevande, i prodotti in metallo e i servizi legali e di contabilità; il sistema a trasmissione gerarchica (trasmissione estesa ma lenta) comprende i settori dei macchinari, del commercio all’ingrosso e dell’alloggio e ristorazione. A trasmissione debole (circoscritta e lenta) risultano, infine, i trasporti terrestri.
I settori dell’industria manifatturiera
Si tratta di un settore ampio, che comprende una pluralità di mercati e ambiti: dalla meccanica, all’alimentare, al tessile, all’elettronica. Un settore in continuo mutamento, per adattarsi da un lato alle mutevoli esigenze del consumo, dall’altro a tecnologie di produzione sempre nuove.
I settori dell’industria manifatturiera censiti dell’Istat sono: alimentari; bevande; tessile; abbigliamento; pelle; legno; carta; stampa; coke e petroliferi; chimica; farmaceutica; gomma e plastica; minerali non metalliferi; metallurgia; prodotti in metallo; elettronica; apparecchiature elettriche; macchinari; autoveicoli; altri mezzi di trasporto; mobili; altre manifatturiere; riparazione e manutenzione di macchinari e apparecchiature.
Che cosa si intende per innovazione nel manifatturiero
Da qualche anno a questa parte quando si parla di innovazione per il manifatturiero si pensa immediatamente al Piano Industria 4.0 e in particolare alla dimensione di innovazione digitale. In realtà la lettura delle possibilità di innovazione deve essere più ampia e deve comprendere sempre e comunque sia i piani di innovazione “tradizionale”, ovvero l’automazione e i processi, sia i processi di innovazione digitale che si allargano a tutte le componenti dell’impresa, ben oltre il solo ambito produttivo.
Ecco che i temi dell’automazione, della robotica, dei sistemi di produzione non solo si arricchiscono di una dimensione legata al valore dei dati, ma permette di attuale una visione integrata, completa e globale – in digitale – di tutti gli asset dell’azienda.
L’Industria 4.0 o Industry 4.0? non è solo una nuova rivoluzione industriale, ma nella forma di digitalizzazione del settore manifatturiero rappresenta un cambiamento radicale, che sta trasformando il modo di lavorare delle fabbriche e che permette di cambiare il rapporto tra i prodotti e i consumatori.
Se si fa un passo indietro si vede che una ricerca di qualche anno fa di McKinsey evidenziava che erano pochi i manager con le idee chiare a riguardo. Anche se per tutti iniziava ad essere evidente che l’Industria 4.0 era guidata da quattro importanti cambiamenti:
l’aumento del volume di dati, della potenza di calcolo e della connettività; lo sviluppo di analytics e soluzioni di business intelligence; nuove forme di interazione uomo-macchina come le interfacce touch e i sistemi di realtà aumentata; il miglioramento nel trasferimento di istruzioni digitali al mondo reale come le stampanti 3D. Lo sviluppo di nuove soluzioni robotica avanzata, l’innovazione a livello di sensoristica IoT
Il futuro del manifatturiero? Le persone
Più recentemente sempre McKinsey metteva in evidenza che se è vero che le nuove tecnologie del digitale stanno assumendo sempre maggiore importanza a livello di produzione è altrettanto vero che il loro valore si concretizza in risultati nel momento in cui è accompagnato da una corrispondente crescita nelle competenze delle persone, ovvero di tutto il personale coinvolto nella produzione. Dai Big Data Analytics per ottimizzare i cicli di produzione a linee di produzione sempre più automatizzate per arrivare a operatori che svolgono le loro mansioni sui prodotti o sugli strumenti di produzione con una dotazione di strumenti di Virtual, Augmented o Virtual Reality. In tutti i casi servono competenze sempre più adeguate sia a livello di prodotto sia a livello di processo.
Come mette in evidenza il post di McKinsey che potete leggere QUI il grande tema del manifatturiero si chiama fattore umano, tanto che si stima che il 60% delle attualità attività manifatturiere potrebbe essere già automatizzata, mentre per quanto riguarda l’automazione dei processi occorre molto più tempo. Nello stesso tempo si osserva che anche le compagnie che operano in settori che hanno spinto sull’automazione continuano ad attribuire grandissima importanza alla forza lavoro delle persone. In particolare sono sempre le persone che gestiscono, correggono, perfezionano gli asset di produzione.
Il manifatturiero che si prepara all’Industria 4.0
Molte di queste tecnologie stanno tentando di emergere da anni, alcune non sono ancora pronte per essere adottate su larga scala, ma tutti dovranno tenerne conto nell’immediato futuro. Da una ricerca McKinsey di qualche anno fa condotta su 300 manager del settore manifatturiero, risultava che solo il 48 per cento si dice pronto per l’Industria 4.0. Uno scenario che sembra recentemente cambiato anche in ragione delle crescente importanza del ruolo e delle competenze assegnate alle persone.
Alcune aziende hanno già iniziato ad integrare i principali trend, come la società di logistica Knapp AG che ha adottato cuffie per la realtà aumentata, consentendo ai lavoratori di veder proiettati gli oggetti da prendere su uno schermo. In questo modo diventa più facile individuare la merce da trasportare e imballare. Local Motors, ad esempio, sta creando rapidamente macchine quasi interamente attraverso le stampanti in 3D, facendo ricorso per il design al crowdsourcing da una community online. Non ci sia aspetta di vedere realizzati questi cambiamenti con la stessa velocità del settore consumer e soprattutto non ci saranno investimenti tali da poter completamente cambiare i macchinari della catena di produzione. Tuttavia, gli intervistati da McKinsey prevedono la sostituzione del 40/50 per cento delle macchine attualmente in uso.
Una bussola digitale per il manifatturiero in chiave 4.0
Le potenzialità dell’Industria 4.0 potranno svelarsi soltanto se si eseguiranno le giuste strategie per il reperimento, trasferimento e corretto utilizzo dei dati. La maggior parte degli executive intervistati da McKinsey è convinta che correggendo le attuali inefficienze nella raccolta e trattamento dei dati si potrebbe incrementare la produttività del 25 per cento.
Ma quali sono le informazioni che danno i maggiori vantaggi? Quali sono le perdite di dati più rischiose? Quali tecnologie possono dare i maggiori rendimenti all’azienda? Per orientare le scelte aziendali nella giusta direzione, McKinsey ha ideato una specie di “bussola digitale”, con otto ambiti in cui creare valore:
Resource /Process;
Asset utilization;
Labor;
Inventories;
Quality;
Supply/Demand match;
Time to market;
Service/aftersales)
e 26 servizi offerti dall’Industria 4.0. Ad esempio, tra questi si trovano strumenti per un consumo più razionale di energia, sistemi di conservazione di informazioni in “lotti intelligenti” e l’ottimizzazione dei rendimenti in tempo reale.
Nuovi modelli di business a consumo che coinvolgono il settore manifatturiero
Il tradizionale business model del settore della produzione sta cambiando e le aziende devono saper individuare i nuovi modelli e scegliere quelli più confacenti alla loro vision per poter stare al passo con il mercato. L’84 per cento dei manager intervistati, infatti, prevede l’ingresso di nuovi competitor a breve. Tra le novità a cui prestare attenzione ci sono sicuramente le piattaforme, nelle quali i prodotti, i servizi e le informazioni possono essere scambiati secondo flussi predefiniti. Basti pensare ai software open-source applicati al settore della produzione: ad esempio, un’azienda potrebbe utilizzare questa tecnologia per connettere varie parti della produzione e consentire un’interazione tra di loro. È quello che ha fatto SLM Solutions, una società produttrice di stampanti 3D, insieme con Atos, una compagnia di servizi IT, lanciando un progetto pilota che mette il consumatore in diretta connessione con gli altri anelli della catena, fino alla consegna del prodotto.
L’Industria 4.0 permetterà anche di lanciare servizi pay-by-use e a sottoscrizione, trasformando i macchinari CAPEX a OPEX. Rolls-Royce è tra le prime ad aver sperimentato questo approccio nel business dei motori dei jet. Molte aziende manifatturiere, infatti, hanno sviluppato una grande esperienza sui loro prodotti e processi ma non sanno trarre valore dai dati accumulati. Per questo motivo, potrebbero monetizzare attraverso la concessione della proprietà intellettuale dei loro prodotti, offrendo consulenza per dare valore alla loro esperienza. Un ultimo aspetto dell’Industria del futuro sarà la possibilità di monetizzare i dati. SCiO, un progetto nato su Kickstarter, distribuisce uno spettrometro tascabile che, mediante tecnologia a infrarossi, può rivelare la composizione dei materiali. Il tutto a un costo di 250 dollari contro i 10 mila dei macchinari in uso a livello industriale. Il vantaggio è che ogni volta che viene utilizzato, SCiO aggiorna il suo database con nuovi materiali e implementa le sue funzionalità. Tutto questo permette poi di aprire nuove prospettive anche in termini di modelli di business come nel caso della servitization, ovvero della possibilità di attuare forme di service transformation in cui il valore per gli utenti e per i clienti non è più nel possesso ma è nella possibilità di disporre dei servizi che arrivano grazie all’utilizzo di un prodotto che resta in capo ad altri soggetti e che grazie ai dati e alle reti (e in questo senso un ruolo importante è svolto dalle reti ibride anche di tipo Sd Wan) permette di remotizzare funzionamento e gestione dei prodotti.
Gestione dei dati e sicurezza priorità del manifatturiero
Per prima cosa, però, le aziende devono preparare la strada per la trasformazione digitale, individuando le competenze mancanti e cercando di riorganizzare la loro struttura in base alle nuove esigenze. La gestione dei dati e la cybersecurity saranno le sfide principali.
E’ certamente importante leggere il tema Industria 4.0 nella prospettiva dei piani di sviluppo di Paesi e Governi che hanno una fortissima vocazione nel manifatturiero e che possono trovare nell’Industry 4.0 una nuova fonte di vantaggi competitivi. In questo senso va letto il Piano Industry 4.0 per l’Italia che attribuisce un ruolo strategico dell’IoT così come il tema dell’Industry 4.0 e delle partnership che contraddistingue la politica industriale tedesca. ma è anche da leggere il grandissimo e importante lavoro sul territorio che vede la creazione di modelli Industry 4.0 sul territorio ad esempio con il lavoro che sta iniziando tra Ferrari e Dallara per una MotorValley di eccellenza nell’Industry 4.0, IoT e innovazione.
Arriva dall’Internet of Things una fonte di dati di produzione per il manifatturiero
Le prospettive dell’IoT relativamente all’Industry 4.0 lasciano intravvedere una forte potenzialità di sviluppo. L’Internet of Things in Italia è arrivato nel corso del 2019 a 6,2 miliardi. Smart Metering e Smart Asset Management nelle utility sono il primo segmento del mercato IoT, con un valore di 1,7 miliardi di euro (+19% rispetto al 2018), pari al 27% del fatturato complessivo, spinto soprattutto dagli obblighi normativi, che hanno portato nel 2019 all’installazione di 3,2 milioni di contatori smart gas (il 58% del totale) e di 5,7 milioni di smart meter elettrici (il 37% di tutti i contatori elettrici). Seguono la Smart Car, che vale 1,2 miliardi di euro (19% del mercato, +14%) e conta 16,7 milioni di veicoli connessi, e lo Smart Building, con un valore di 670 milioni (+12%), legato principalmente alla videosorveglianza e alla gestione dei consumi energetici negli edifici.
Secondo il Direttore dell’Osservatorio Internet of Things, della School of Management del Politecnico di Milano Giovanni Miragliotta tutto il settore del manufacturing potrà dare vita a nuove forme di efficienza e soprattutto potrà esplorare e sviluppare nuovi modelli di business come evidenziato nell’articolo: Miragliotta: il potenziale dell’Industry 4.0 .
Sono sempre più numerosi i casi di realtà che grazie all’Industria IoT e ai progetti di Industry 4.0 hanno potuto inventare e definire nuovi modelli di business e affermarsi come case history di riferimento per l’Industria 4.0. Si può pensare a GS1 Italy e al progetto che permette di avere treni e vetture sotto controllo con l’IoT; oppure alla macchina per la preparazione del caffè connessa di Cimbali; o ancora all’automatizzazione nell’healthcare con Inpeco. Ma ci sono tanti altri casi che riguardano anche la vita di tutti i giorni e le nostre case dove ad esempio la sicurezza e il consumo energetico sono sempre più importanti. BTicino e Qlik, con l’IoT applicato agli interruttori hanno sviluppato una soluzione per abbattere i consumi energetici e siamo nel terreno dello Smart Building. Rimanendo sempre nell’ambito della gestione dei building e dei building intelligenti occorre osservare gli sviluppi del Facility Management e Realt Estate che con l’IoT e il Cognitive Computing ha cambiato completamente la propria prospettiva di gestione e di erogazione dei servizi. Un esempio in questo senso arriva da IBM che ha sviluppato soluzioni e strategie IoT per cambiare il Facility Management e la gestione del Real Estate, da SAP e Fujitsu che con la loro partnership sull’IoT hanno focalizzato l’attenzione anche sul mondo building automation e smart metering e da Schneider Electric che con l’IoT ha sviluppato soluzioni per l’energy saving e la sicurezza nelle case nella forma di Building Automation.
Le competenze per il nuovo manifatturiero
Di fronte alla quarta rivoluzione industriale il cambiamento che le imprese sono chiamate ad affrontare non si basa soltanto sulle nuove tecnologie: legato a questo aspetto ce n’è un altro che per il panorama italiano, composto in gran parte da piccole e medie imprese, è altrettanto impegnativo: quello delle competenze.
Se infatti secondo i dati dell’osservatorio MecSpe relativo alle Pmi sui primi sei mesi del 2018 la maggior parte del campione ritiene che non assisteremo alla scomparsa delle attuali figure professionali, c’è da aggiungere che alle professioni “tradizionali” se ne stanno rapidamente aggiungendo di nuove, caratterizzate spesso da una alto livello di competenze in ambito IT. Così da qui al prossimo decennio si assisterà a una richiesta sempre più sostenuta, anche e soprattutto nel manifatturiero, di robotic engineers, specialisti in big data, programmatori esperti in intelligenza artificiale, specialisti IoT, multichannel architect ed esperti di cybersecurity.
Di tutto questo personale al momento l’offerta è scarsa, tanto che la maggior parte delle aziende interessate a investire nel cambiamento ne lamentano la carenza. Per questo oggi la ricerca avviene soprattutto tramite agenzie specializzate, ma anche università e istituti tecnici, società di consulenza. E spesso le aziende ricorrono a iniziative di formazione interna per mettere a disposizione dei propri dipendenti più qualificati in questi campi gli strumenti per aggiornarsi e affrontare le nuove sfide dell’industria 4.0.
Tra gli strumenti che potrebbero dare un forte boost allo sviluppo di nuove competenze e all’innovazione all’interno delle fabbriche c’è ovviamente l’Open innovation, che consente alle aziende di entrare in contatto e di unire le forze con piccole realtà iper specializzate, come ad esempio alcune startup innovative, per innovare i propri processi e contribuire a una formazione sul campo dei propri dipendenti: sono così all’ordine del giorno partnership in grado di dare nuove opportunità ai talenti emergenti e di fornire competenze qualificate e all’avanguardia alle società che ne hanno bisogno.
La sperimentazione delle imprese manifatturiere
Che proprio le competenze, insieme alla diffusione di Industria 4.0 nelle Poi, siano i due ostacoli principali che l’Italia si trova ad affrontare è emerso dagli Ey manufacturing lab: “Mentre una una macchina posso acquistarla in 3 settimane – spiega Donato Iacovone, Ad di EY, a ZerounoWeb – per avere una competenza che sappia realmente sfruttare la nuova tecnologia ci vogliono mesi se non anni. Per questo abbiamo contribuito all’Alleanza per il lavoro del futuro, un’iniziativa che coinvolge aziende leader di mercato, università e scuole superiori, con l’obiettivo di creare 100.000 posti di lavoro nei prossimi cinque anni”. Dai dati della società risulta infatti che nel 2017 ci sono state 27mila richieste di personale con competenze tecnologiche di alto livello che non hanno trovato soddisfazione in Italia, mentre 30mila si sono spostate fuori dai confini nazionali.
Secondo un’analisi di Francesco Seghezzi, direttore della fondazione Adapt, pubblicata su Fabbrica Futuro, “il nuovo scenario richiede rapide e precise azioni di riqualificazione e formazione continua per poter adattare la forza lavoro ai nuovi processi (…) Se infatti le tecnologie si evolvono molto rapidamente, con esse aumenta il rischio di obsolescenza di competenze fino a poco tempo prima fondamentali. (…) Risulta dunque più importante la capacità di adattamento e di apprendimento di nuovi processi che nel corso del tempo si affermano rispetto alla conoscenza dettagliata di strumenti che in pochi anni scompaiono”. Se si volesse così comporre l’identikit delle figure professionali più richieste ai tempi di industria 4.0, ne scaturirebbe “l’esigenza di soggetti integrali piuttosto che di specialisti. Lo scenario di complessità, che Industria 4.0 rappresenta in modo efficace, esige persone in grado di sapersi orientare all’interno di tale scenario, e questo riguarda la gestione dei processi, ma anche dimensioni più personali come la gestione di tempi e luoghi di lavoro all’interno di una realtà che rischia di fagocitare tutti in un circolo di iper-connessione costante”.
I Big data per la manifattura digitale
L’utilizzo dei dati per dare vita a nuove opportunità nel settore manifatturiero è uno dei pilastri della cosiddetta industria 4.0, e spesso rappresenta proprio la parte finale del percorso che porta alla connessione dei macchinari e all’utilizzo delle tecnologie digitali più all’avanguardia negli ambienti produttivi. I macchinari connessi, infatti, oltre a poter essere comandati a distanza e a rappresentare l’ultima frontiera dell’automatizzazione, producono dati che se opportunamente integrati e analizzati possono aprire nuove opportunità di business o di razionalizzazione e contenimento dei costi.
Da queste considerazioni nascono tutta una serie di definizioni che sempre più spesso vengono utilizzate per indicare l’utilizzo delle informazioni raccolte, dal Manufacturing big data all’advanced manufacturing, dall’industrial analytics allo smart manufacturing.
Ad abilitare l’utilizzo in tempo reale dei dati nella filiera produttiva è nella maggior parte dei casi l’internet of things, cioè gli oggetti e le macchine connesse che sono in grado di trasmettere in tempo reale tutte le informazioni sul proprio funzionamento, abilitando così ad esempio soluzioni di manutenzione predittiva, che sono in grado di interpretare dati per capire lo “stato di salute” della macchina, e intervenire prima che malfunzionamenti interrompano il processo di produzione.
Il meccanismo “virtuoso” che si innesca abbracciando l’opportunità della convergenza tra i sistemi “tradizionali” del mondo della produzione industriale, che sono nella maggior parte “fisici”, cioè le macchine, e quelli che vengono definiti “virtuali”, quindi digitali, parte dalla produzione dei dati: informazioni che erano in teoria disponibili anche prima, ma che ora possono essere “estratte” e interpretate in tempo reale. Questo consente di poterle analizzare grazie a grandi capacità di calcolo proprio mentre vengono prodotte. Da qui due nuove possibilità: la manutenzione predittiva, che consente – come dicevamo – di intervenire prima che si troppo tardi nel caso di un malfunzionamento. E poi la possibilità riconfigurare i processi nella modalità più corretta e quindi anche meno dispendiosa.
Utilizzare big data nel mondo dell’industria, quindi, può consentire – se si utilizzano le tecnologie nel modo migliore – di ottenere vantaggi su quattro “assi” fondamentali per il business, a partire dalla qualità della produzione, che può essere monitorata e indirizzata ottenendo i risultati migliori volta per volta, intervento sia sul miglioramento della funzionalità, sia sulle prestazioni sia in chiave estetica. La prospettiva di cui si parla già con insistenza è quella di arrivare a una produzione “personalizzata”, a sfornare cioè prodotti che si adattino in modo sempre più deciso alle esigenze dei singoli utenti, senza per questo dover sostenere i costi estremamente alti che si dovevano affrontare finora per apportare cambiamenti al processo di produzione. Un’opportunità che può tradursi immediatamente in più competitività sul mercato. Da considerare inoltre che la digitalizzazione, quando si parla di aumentare la qualità dei prodotti, non si limita a interessare soltanto gli ambienti produttivi, ma arriva a coinvolgere anche il rapporto con gli utenti finali, con i feedback dei consumatori che vengono utilizzati per orientare la produzione.
Il manifatturiero trova nuove forme di efficienza nei Big Data
Il secondo vantaggio dei big data nel manifatturiero si misura in termini di tempo: si riduce infatti in modo deciso l’intervallo che trascorre dalla progettazione alla produzione e all’arrivo sul mercato di un prodotto. Grazie al digitale la prototipazione diventa più agile, questo consente di arrivare in tempi più rapidi alla fase di produzione e di gestirla nel modo più “razionale”, mantenendo sempre il controllo sull’intera supply chain, riducendo quindi al minimo indispensabile le scorte di magazzino e i costi dovuti a questa parte della filiera.
Il terzo effetto tangibile è quello che si verifica sui costi, anche come conseguenza dei due punti appena affrontati: utilizzare l’analisi dei big data nella produzione infatti vuol dire poter programmare l’acquisto e l’utilizzo delle materie prime con bassissimi margini di errore, poter fare affidamento sul fatto che gli scarti siano ridotti ai minimi termine, così come i prodotti “mal riusciti”. Altro settore in cui gli analytics possono essere applicati con risultati importanti è quello dei consumi energetici: avere infatti il quadro completo dell’energia consumata in tempo reale da un impianto produttivo consente di mettere in campo tutta una serie di accorgimenti che possano ridurre i consumi “di picco” e razionalizzare l’utilizzo dell’energia all’interno della fabbrica.
Infine il quarto punto, che è particolarmente “rivoluzionario” rispetto al posto che la fabbrica occupa nell’immaginario collettivo, è la flessibilità. Vuol dire poter “personalizzare” in modo agile la produzione, controllandone il ritmo e potendolo modificare man mano che arrivano nuove informazioni dal mercato e dai consumatori, adattandola anche in real time ai gusti e alle preferenze che emergono dalle indagini di mercato o da feedback dei consumatori.
Il piano industria 4.0: cosa cambia per il manifatturiero
Con la finanziaria 2019 il governo ha ripreso il filo del piano industria 4.0 varato dall’esecutivo precedente, per una scelta di sostanziale continuità rispetto agli incentivi alle imprese. Così la manovra, approvata allo scadere del 2018, ha destinato una serie di incentivi per industria 4.0 e tecnologie di nuova generazione.
Nell’ambito dello smart manufacturing la principale novità è rappresentata dal cloud, con una maggiorazione del 140% alla deducibilità dei canoni pagati per servizi e software fruiti sul cloud: di questo provvedimento si era fatta portavoce Confindustria digitale.
Sul fronte iperammortamento, slittano di un anno le scadenze della maggiorazione per gli investimenti 4.0, che così coprirà anche gli ordini effettuati dal 1 gennaio 2019 al 31 dicembre 2019 con consegna entro 31 dicembre 2020. Quanto alle aliquote, fissato il 270% per i progetti fino a 2,5 milioni; 200% per quelli tra 2,5 e 10 milioni; 150% per quelli tra 10 e 20 milioni, con un tetto massimo per gli investimenti pari a 20 milioni, oltre i quali non ci si può avvantaggiare della maggiorazione. Per i beni immateriali inoltre l’incentivo è stato confermato al 140%.
Fissate a 480 milioni le risorse per la nuova Sabatini, mentre sul fronte credito di imposta per l’R&S il tetto massimo scende da 20 a 10 milioni mentre l’aliquota passa dal 50% al 25%. Il bonus resta del 50% per le spese che riguardano il personale dipendente e per i contratti stipulati con università, enti di ricerca e startup innovative.
Viene rinnovato il credito d’imposta per le attività di formazione con tre aliquote diversificate per dimensione di impresa: 50% per le piccole con un tetto massimo di 300.000 euro, 40% per le medie imprese e 30% per le grandi con un tetto di 200.000 euro per azienda.
Il ruolo dell’innovation manager nelle imprese manifatturiere
Viene inoltre introdotto un voucher per l’Innovation Manager è introdotto per “sostenere i processi di trasformazione tecnologica e digitale attraverso le tecnologie abilitanti previste dal Piano Nazionale Impresa 4.0 e di ammodernamento degli assetti gestionali e organizzativi dell’impresa, compreso l’accesso ai mercati finanziari e dei capitali”. Si tratta di un incentivo a fondo perduto pari a 40.000 euro per le micro e piccole imprese nel limite del 50% della spesa; 25.000 euro per le medie imprese nel limite del 30% della spesa; 80.000 euro per le reti d’impresa nel limite del 50% delle spese sostenute. Sul piatto 25 milioni di euro all’anno.
Sulla microelettronica, il provvedimento istituisce “un fondo finalizzato all’erogazione dei contributi alle imprese che partecipano alla realizzazione dell’importante progetto di interesse comune europeo (Ipcei) sulla microelettronica, con una dotazione di 50 milioni di euro per ciascuno degli anni 2019 e 2020, di 60 milioni di euro per il 2021 e di 83,4 milioni di euro per ciascuno degli anni dal 2022 al 2024″.
Con il “decreto crescita” che con il mese di marzo è allo studio dei tecnici del Mef, inoltre, il Governo ha in programma di introdurre una serie di altre agevolazioni e nuove risorse grazie a una “Sabatini quater”, che prevede la concessione di un contributo del Mise a sostegno delle Pmi che investono in tecnologie digitali. La nuova misura prevede, secondo le prime indiscrezioni, la cancellazione del tetto massimo del finanziamento ammesso al contributo, attualmente di due milioni di euro, e l’erogazione del contributo in un’unica soluzione, Per semplificare le procedure, inoltre, i controlli anziché preventivi, come accade oggi, sarebbero rinviati a una seconda fase.
quanto al superammortamento, il provvedimento prevede che sia reintrodotto da aprile fino alla fine del 2019 quello al 130% degli investimenti in beni strumentali a eccezione di autovetture, immobili, attrezzature di lunga durata e beni immateriali. Inoltre il credito di imposta R&S, in scadenza a fine 2020, è prorogato per il triennio 2021-2023.
Il trend: boom di robot e automazione nel manifatturiero Usa
Che la corsa all’automazione nelle fabbriche sia ormai partita a ritmo sostenuto lo dimostrano alcuni dati che provengono dal mercato statunitense, dove nel 2018 le vendite di robot industriali alle imprese hanno raggiunto la soglia record di 28.478 unità, segnando un + 16% nei confronti dell’anno precedente. A scattare la fotografia è l’Association for advancing automation, secondo cui i principali vantaggi che spingono le aziende in questa direzione sono l’abbattimento dei costi e la flessibilità. L’adozione di queste tecnologie, secondo la ricerca, riguarda imprese di tutte le dimensioni e di tutti i segmenti produttivi. Sorprende in questo contesto, il caso dell’acquisto di robot nell’automotive: per la prima volta dal 2010 per il settore auto e componenti rappresenta infatti meno del 50% degli acquisti totali di robot industriali: un calo importante se si considera che lo scorso anno la percentuale era al 60%.
A crescere con forza nell’adozione di robot sono invece il comparto food e beni al consumo, dove gli acquisti sono cresciuti del 60%, insieme all’elettronica e ai semiconduttori, con un +50%.
Secondo l’analisi dell’associazione questo trend potrebbe essere una conseguenza delle politiche dell’America first del presidente Donald Trump: le misure con cui Trump spinge a riportare negli Stati Uniti larghe fette della produzione industriale potrebbero infatti aver convinto molte aziende a automatizzare il più possibile le operazioni in fabbrica per evitare assunzioni in massa di manodopera negli Usa.
Sull’innovazione digitale per il mondo delle PMI manifatturieri suggeriamo la lettura del servizio dedicato a come Cloud, nuovi competenze e sicurezza possono far crescere la competitività del manifatturiero
Articolo aggiornato da Mauro Bellini il 15 Febbraio 2020
Articolo aggiornato da Pierluigi Sandonnini il 18 Maggio 2020
Immagine fornita da Shutterstock
Post a Comment